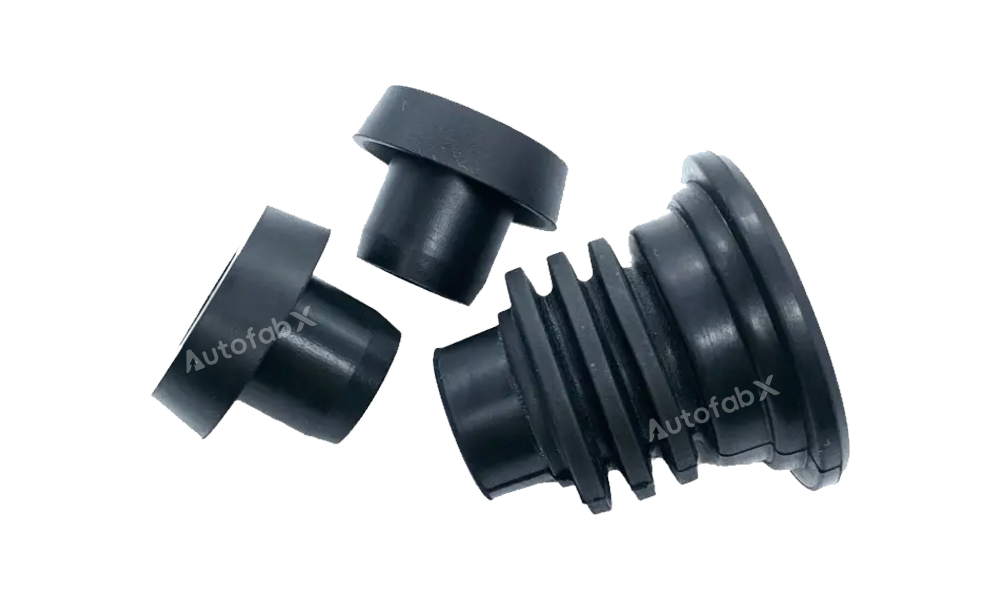
Quick Look
Hardness | Tensile Strength (Mpa) | Elongation at Break, % | Tear strength (KN/m) | 70°C Demold time |
---|---|---|---|---|
85-90 Shore A | 16-18 | 420-450 | 22-25 | 90-120min |
About the Material
Here’s an overview of the Rubber-Like material for Urethane Casting on the AutofabX platform, including its advantages, limitations, physical properties, design parameters, and more:
Rubber-Like Material Advantages:
Elasticity: Rubber-Like materials are highly flexible and elastic, allowing them to be used in applications that require parts to deform and return to their original shape.
High Tear Resistance: They offer good tear strength, making them ideal for parts that will be subject to mechanical wear and stress.
Excellent Impact Resistance: Rubber-Like materials absorb impact well, making them suitable for parts that will experience frequent shocks or high stress.
Vibration Damping: Due to their flexibility and elasticity, Rubber-Like materials can dampen vibrations, making them useful for noise-reducing applications or in environments where mechanical vibrations are a concern.
Low Coefficient of Friction: These materials have a lower coefficient of friction compared to many rigid plastics, making them ideal for applications involving moving parts.
Rubber-Like Material Limitations:
Lower Dimensional Stability: Rubber-Like materials can deform or change shape under heat or load over time, which can be a limitation for precision applications.
Chemical Resistance: While they offer good resistance to wear, their chemical resistance may be limited when exposed to aggressive solvents or oils, depending on the specific formulation.
Surface Finish: Achieving a smooth, glossy finish on Rubber-Like materials can be challenging, as they tend to have a more matte or textured surface.
Heat Resistance: Rubber-Like materials are not typically suitable for high-temperature applications, as they may degrade or lose flexibility when exposed to elevated temperatures (above 80-100°C).
Physical Properties Table for Rubber-Like Material:
Property | Value/Description |
Hardness (Shore A) | 30-80 |
Density | 1.10-1.30 g/cm³ |
Cubic Inches per Pound | 19-26 |
Color | Black, Custom Colors |
Tensile Strength | 5-20 MPa |
Tensile Modulus | 50-300 MPa |
Elongation at Break | 100-600% |
Flexural Strength | 5-30 MPa |
Flexural Modulus | 50-200 MPa |
Shrinkage (linear) | 0.5-1.0% |
Impact Strength | 20-50 kJ/m² |
Bending Strength | 5-20 MPa |
Glass Transition Temperature | -20 to -50°C |
Maximum Pouring Thickness | 10-15 mm |
Demold Time | 2-4 hours |
Chemical Properties Table:
Property | Value/Description |
Water Absorption | Moderate |
Acid Resistance | Moderate |
Alkali Resistance | Low |
Oil Resistance | Moderate to Good |
Solvent Resistance | Moderate |
Design Parameters:
Maximum Bulid Size (mm) | Minimum Wall Thickness (mm) | Minimum Assembly Gap (mm) | Tolerance | Minimum End Mill Size (mm) | Minimum Drill Size (mm) |
500x500x500 | 1 | 0.2 | 0.50% | / | / |
Industry Applications and Customer Case Studies:
Automotive: Rubber-Like materials are used in automotive parts such as seals, gaskets, bumpers, and vibration dampers, where elasticity, impact resistance, and vibration absorption are needed.
Consumer Goods: Common in the production of flexible parts like grips, handles, and non-slip feet, which require flexibility and durability.
Medical Devices: Suitable for non-invasive medical components such as seals, grips, and soft-touch components, where flexibility and biocompatibility are important.
Electronics: Used for parts like buttons, protective covers, and dampers, offering flexibility and protection to sensitive electronic components.
Industrial Applications: Rubber-Like materials are used in industrial equipment for gaskets, seals, and protective casings, requiring high durability and flexibility under mechanical stress.
Frequently Asked Questions (FAQs):
What is the temperature range for Rubber-Like materials?
Rubber-Like materials typically perform well at temperatures between -20°C and 80°C, but prolonged exposure to temperatures above 100°C can degrade the material.
Are Rubber-Like materials resistant to oils and solvents?
Rubber-Like materials have moderate resistance to oils and solvents, but their chemical resistance may not be as high as other materials. Testing should be done for specific applications.
Can Rubber-Like materials be used for high-stress applications?
While Rubber-Like materials are excellent for applications involving flexibility and impact resistance, they are not suitable for high-stress applications requiring rigid strength. Higher-performance elastomers may be needed in such cases.
Is Rubber-Like material UV resistant?
Rubber-Like materials can degrade with prolonged UV exposure, especially if not treated or coated. Protective coatings or UV-resistant treatments should be applied for outdoor applications.
What is the demold time for Rubber-Like materials?
Demold time typically ranges from 2 to 4 hours, depending on part size, thickness, and mold design.
Can Rubber-Like materials be used for food-contact applications?
Rubber-Like materials are generally not food-safe unless explicitly specified by the manufacturer. For food-safe applications, alternative materials or specific certifications should be considered.
Rubber-Like materials are ideal for applications requiring flexibility, impact resistance, and vibration damping, but they are not suitable for high-precision or high-temperature applications. They provide excellent value for prototyping and functional parts in a variety of industries.
Finishing Options

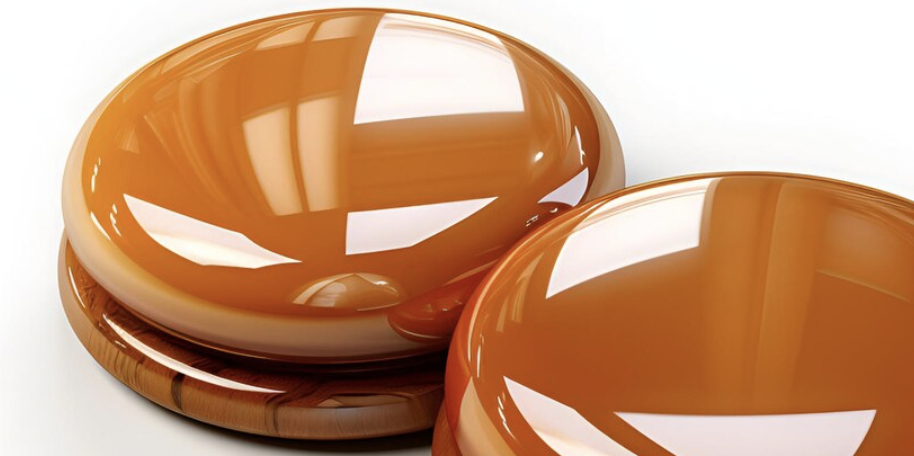
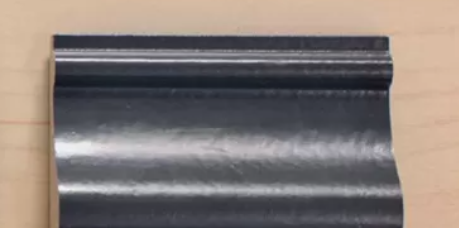
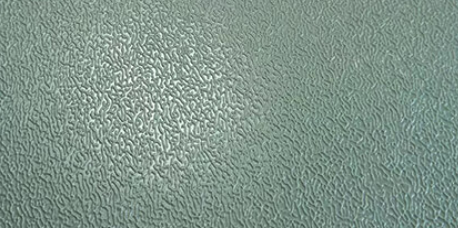

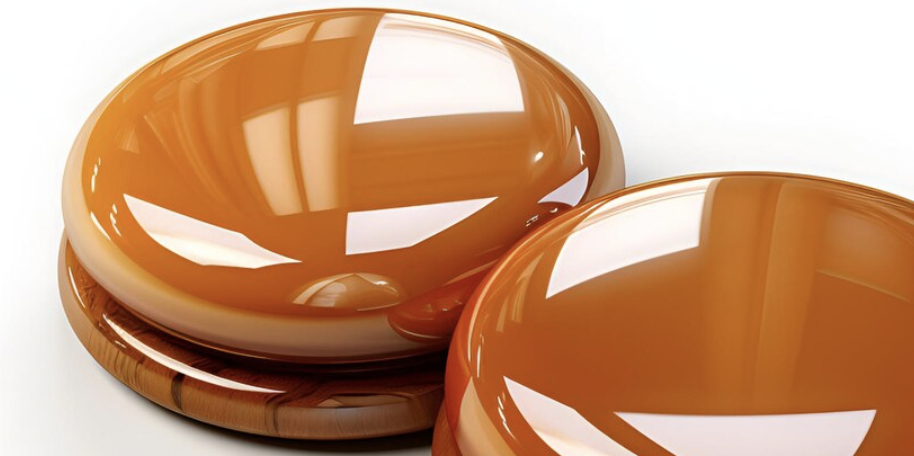
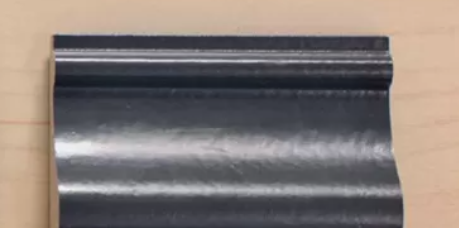
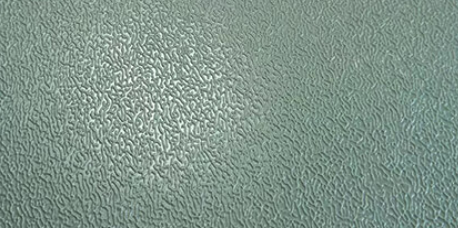
Parts Made by AutofabX
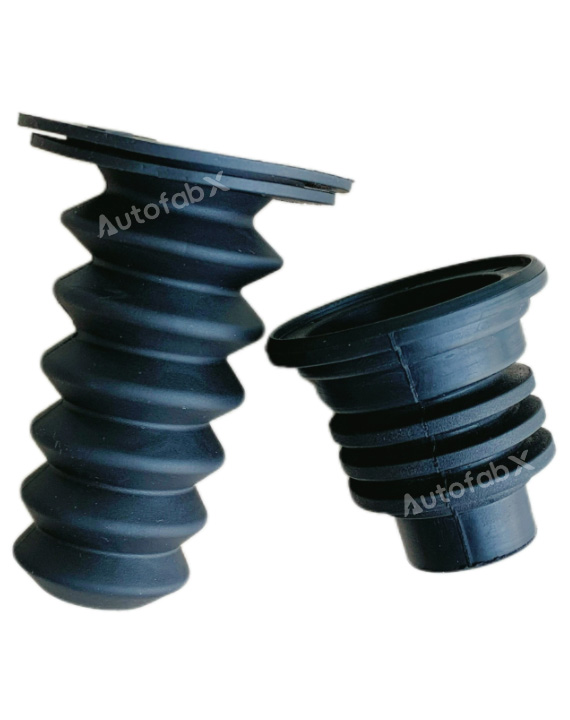