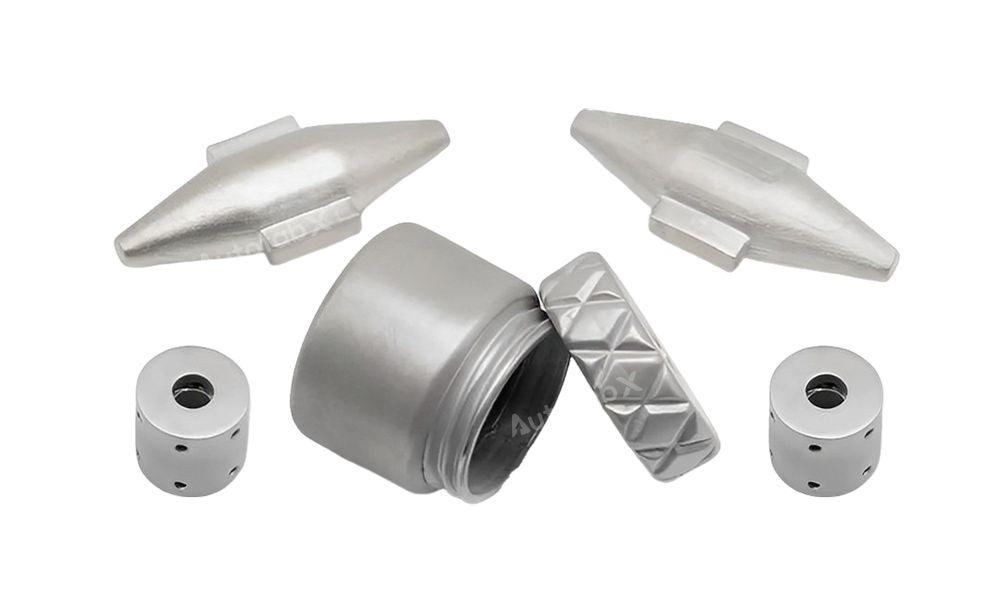
Quick Look
Alloy Number | Density(g/cm3 ) | Rockwell Hardness | Tensile Strength(MPa) | Elongation(%) |
---|---|---|---|---|
95%W-Ni-Fe | 18.1 | 30 | 960 | 25 |
97%W-Ni-Fe | 18.5 | 33 | 940 | 15 |
About the Material
Advantages:
High Density: Tungsten alloys have a high density, making them ideal for applications requiring significant weight in a small volume, such as counterweights and radiation shields.
Radiation Absorption: Due to their high atomic number, tungsten alloys are effective at shielding against radiation, suitable for medical and nuclear industries.
Thermal Stability: Tungsten alloys maintain strength and stability at high temperatures, making them suitable for aerospace and high-temperature industrial applications.
Good Wear Resistance: Tungsten alloys provide excellent wear resistance, which is beneficial for parts subjected to friction and wear, such as cutting tools.
Vibration Damping: Tungsten alloys have good vibration damping capabilities, useful for reducing vibrations in sensitive equipment.
Limitations:
High Cost: The cost of tungsten and the complexity of processing can be higher compared to other materials, limiting its use to specialized applications.
Brittleness: Tungsten alloys can be brittle, which may limit their use in applications requiring high impact resistance.
Machining Difficulty: Tungsten alloys are difficult to machine due to their hardness and high density, requiring specialized tools and techniques.
Size Limitations: Similar to other MIM materials, tungsten alloys are typically used for small to medium-sized components.
Complex Debinding and Sintering: The debinding and sintering process for tungsten alloys can be challenging, requiring precise control to avoid defects.
Chemical Properties Table
Alloy Type | Tungsten (W) | Nickel (Ni) | Iron (Fe) | Cobalt (Co) | Molybdenum (Mo) | Other Elements |
W-Ni-Fe | 90-97% | 2-4% | 1-3% | — | — | Copper (Cu), Phosphorus (P) |
W-Ni-Cu | 90-95% | 4-6% | — | — | — | Copper (Cu), Phosphorus (P) |
W-Ni-Co | 90-95% | 3-5% | — | 2-4% | — | Phosphorus (P), Sulfur (S) |
Machining Properties Table
Alloy Type | Machinability Rating | Cutting Speed (m/min) | Tool Wear Resistance | Coolant Requirement | Hardness (HRC) | Surface Finish Quality |
W-Ni-Fe | Low | 10-20 | High | Required | 35-45 | Fair |
W-Ni-Cu | Low | 10-25 | High | Required | 30-40 | Fair |
W-Ni-Co | Low | 10-20 | Very High | Required | 40-50 | Fair |
Metal Injection Molding Tungsten Alloys Design Parameters
Maximum Bulid Size (mm) | Minimum Wall Thickness (mm) | Minimum Assembly Gap (mm) | Tolerance (mm) | Minimum End Mill Size (mm) | Minimum Drill Size (mm) |
200x100x100 | 1 | 0.1 | 0.1 | / | / |
Industry Applications and Case Studies for MIM Tungsten Alloys:
Medical Industry:
Application: Production of radiation shielding components for medical imaging equipment.
Case Study: A medical equipment manufacturer used MIM tungsten alloys to produce compact radiation shields for X-ray devices, enhancing safety while reducing the overall size of the equipment.
Aerospace Industry:
Application: Manufacturing of high-temperature resistant components for jet engines and spacecraft.
Case Study: An aerospace company utilized MIM tungsten alloys to produce nozzle parts for jet engines, which required materials capable of withstanding extreme temperatures and pressures.
Automotive Industry:
Application: Counterweights for engine components to reduce vibration.
Case Study: An automotive manufacturer employed MIM tungsten alloys to create counterweights for crankshafts, effectively reducing engine vibrations and improving overall performance.
Industrial Tooling:
Application: Production of cutting tools and wear-resistant parts.
Case Study: An industrial tooling company used MIM tungsten alloys to produce wear-resistant cutting inserts, extending tool life and reducing downtime for replacement.
Defense Industry:
Application: Fabrication of penetrators and ballistic components.
Case Study: A defense contractor utilized MIM tungsten alloys to produce kinetic energy penetrators, benefiting from the high density and strength of tungsten to improve armor-piercing capabilities.
Frequently Asked Questions (FAQs) about MIM Tungsten Alloys:
What are the common applications of MIM tungsten alloys?
Common applications include radiation shielding, aerospace components, automotive counterweights, industrial cutting tools, and defense-related parts.
What are the benefits of using tungsten alloys in MIM?
Tungsten alloys provide high density, radiation absorption, thermal stability, wear resistance, and vibration damping, making them ideal for specialized applications.
What are the limitations of MIM tungsten alloys?
Limitations include high cost, brittleness, machining difficulty, size constraints, and the complexity of the debinding and sintering process.
Are MIM tungsten alloys suitable for radiation shielding?
Yes, MIM tungsten alloys are highly effective for radiation shielding due to their high density and atomic number, making them suitable for medical and nuclear applications.
How do MIM tungsten alloys perform at high temperatures?
Tungsten alloys maintain their strength and stability at elevated temperatures, making them suitable for high-temperature applications in aerospace and industrial environments.
Can MIM tungsten alloys be used for vibration damping?
Yes, tungsten alloys have good vibration damping properties, which are beneficial for reducing vibrations in sensitive equipment or automotive components.
What industries benefit from MIM tungsten alloys?
Industries such as medical, aerospace, automotive, industrial tooling, and defense benefit significantly from the use of MIM tungsten alloys due to their unique properties.
What are the challenges in machining MIM tungsten alloys?
Tungsten alloys are difficult to machine due to their hardness and density, requiring specialized tools and techniques to achieve the desired precision and finish.
Finishing Options
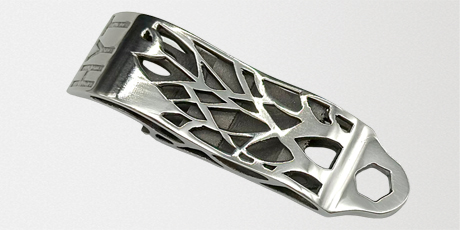
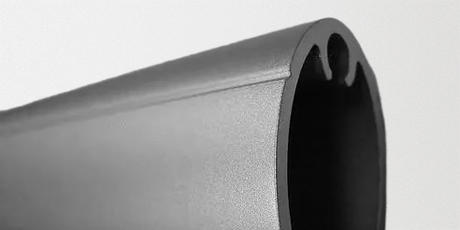
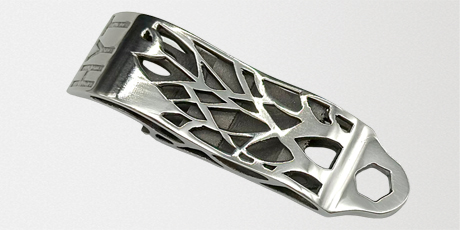
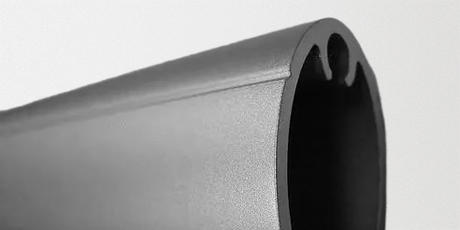
Parts Made by AutofabX
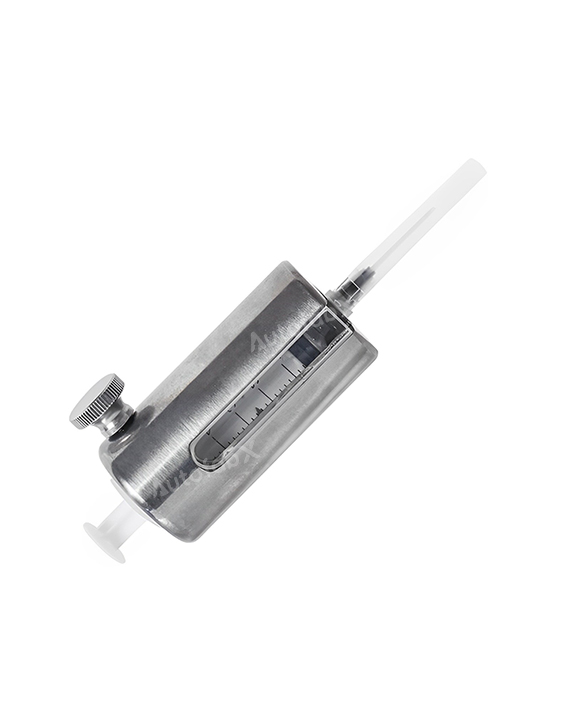
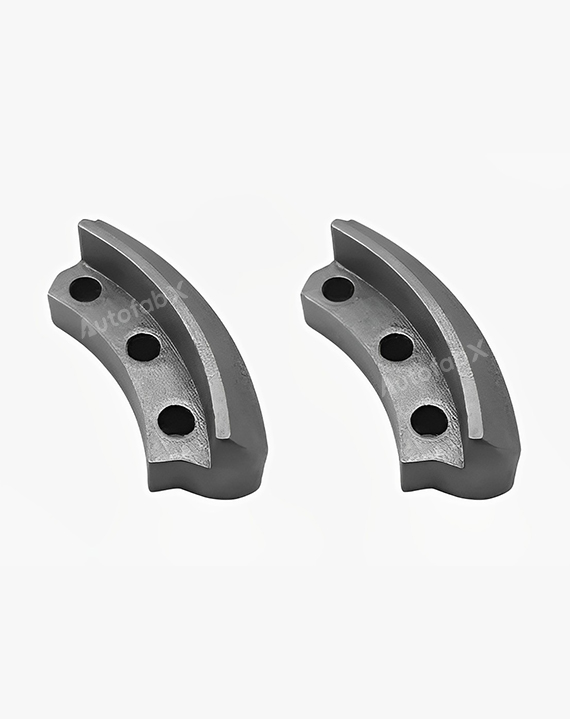