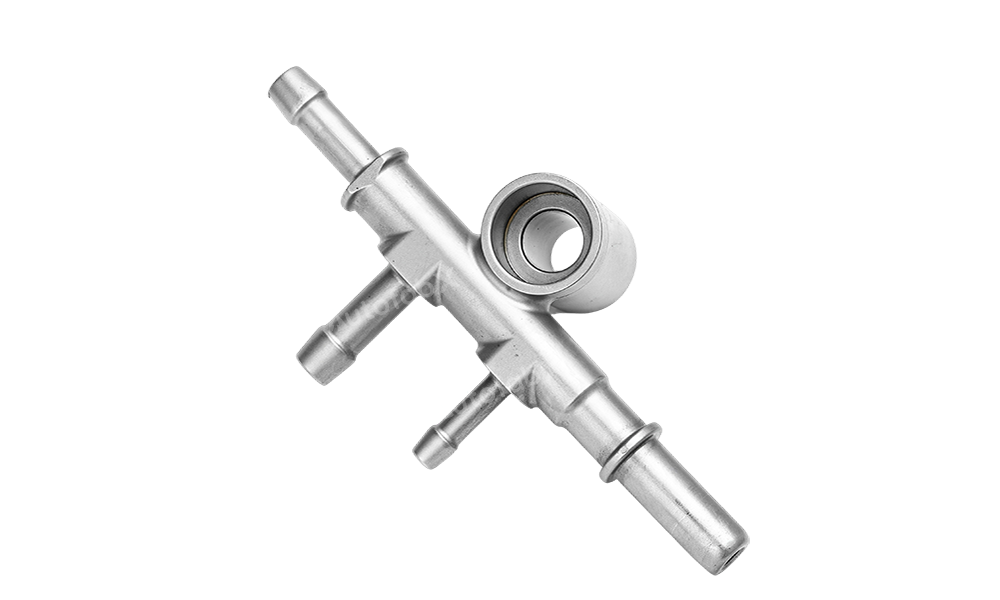
Quick Look
Alloy Number | Density(g/cm3 ) | Rockwell Hardness | Tensile Strength(MPa) | Elongation(%) |
---|---|---|---|---|
MIM - 316L (Sintered) | 7.92 | 67HB | 520 | 50 |
MIM- 17-4PH (Sintered) | 7.5 | 27HRC | 900 | 6 |
MIM- 17-4PH (Tempering) | 7.5 | 40HRC | 1185 | 6 |
About the Material
Advantages:
Corrosion Resistance: MIM stainless steel alloys such as 316L provide excellent corrosion resistance, suitable for harsh environments.
Biocompatibility: Stainless steel is ideal for medical applications, such as implants and surgical instruments, due to its biocompatibility.
High Strength and Durability: Provides high tensile strength, suitable for mechanical and structural applications.
Complex Geometries: The MIM process allows for intricate designs that are challenging to achieve through traditional methods, enabling innovative product designs.
Aesthetic Surface Finish: Stainless steel can achieve a high-quality surface finish, making it ideal for consumer-facing products.
Cost-Effective for High Volumes: The MIM process is cost-efficient for producing large quantities of stainless steel parts, reducing waste and minimizing secondary machining.
Limitations:
High Initial Tooling Costs: The setup and tooling costs are high, making MIM less suitable for low-volume production.
Size Limitations: MIM is typically used for small to medium-sized parts, with limitations on producing very large components.
Debinding Complexity: The debinding process for stainless steel can be complex and time-consuming, requiring precise control to avoid defects.
Material Restrictions: Not all grades of stainless steel are suitable for the MIM process, limiting material choices compared to other manufacturing methods.
Potential Porosity: Residual porosity may affect the mechanical properties of MIM stainless steel parts, necessitating additional processing in some cases.
Chemical Properties Table
Alloy Type | Carbon (C) | Chromium (Cr) | Nickel (Ni) | Molybdenum (Mo) | Manganese (Mn) | Silicon (Si) | Other Elements |
316L Stainless | 0.03% max | 16-18% | 10-14% | 2-3% | 2% max | 1% max | Nitrogen (N), Sulfur (S) |
17-4 PH | 0.07% max | 15-17.5% | 3-5% | 0.5% max | 1% max | 1% max | Copper (Cu), Niobium (Nb) |
Machining Properties Table
Alloy Type | Machinability Rating | Cutting Speed (m/min) | Tool Wear Resistance | Coolant Requirement | Hardness (HRC) | Surface Finish Quality |
316L Stainless | Moderate | 30-50 | Good | Required | 25-35 | Good |
17-4 PH | Moderate to High | 40-60 | Very Good | Required | 35-40 | Excellent |
Metal Injection Molding Stainless Steel Design Parameters
Maximum Bulid Size (mm) | Minimum Wall Thickness (mm) | Minimum Assembly Gap (mm) | Tolerance (mm) | Minimum End Mill Size (mm) | Minimum Drill Size (mm) |
200x100x100 | 1 | 0.1 | 0.1 | / | / |
Industry Applications and Case Studies for MIM Stainless Steel:
Medical Devices:
Application: Production of surgical instruments, orthodontic brackets, and implantable devices.
Case Study: A medical device manufacturer used MIM 316L stainless steel to produce minimally invasive surgical tools, achieving high precision and biocompatibility, leading to improved patient outcomes.
Automotive Industry:
Application: Production of fuel system components, exhaust sensors, and turbocharger parts.
Case Study: An automotive supplier utilized MIM stainless steel to produce complex exhaust sensor housings, improving performance and reducing emissions.
Consumer Electronics:
Application: Fabrication of connectors, structural components, and decorative parts.
Case Study: A leading electronics company used MIM stainless steel to create intricate hinges for a premium laptop, providing strength and a sleek appearance.
Aerospace Industry:
Application: Production of lightweight yet strong components for aircraft systems, such as brackets and fasteners.
Case Study: An aerospace company employed MIM stainless steel to manufacture high-strength fasteners for aircraft interiors, reducing weight while maintaining safety standards.
Food Processing Equipment:
Application: Manufacturing of nozzles, fittings, and other components used in food-grade environments.
Case Study: A food equipment manufacturer used MIM 316L stainless steel to produce corrosion-resistant fittings, ensuring compliance with hygiene standards.
Frequently Asked Questions (FAQs) about MIM Stainless Steel:
What are the common types of stainless steel used in MIM?
Common types include 316L and 17-4 PH stainless steel, known for their corrosion resistance and mechanical strength.
What industries benefit most from MIM stainless steel?
Industries such as medical, automotive, aerospace, consumer electronics, and food processing benefit significantly from the use of MIM stainless steel due to its corrosion resistance and strength.
What are the benefits of using stainless steel in MIM?
Stainless steel provides high strength, corrosion resistance, biocompatibility, and the ability to create complex geometries, making it ideal for various applications.
What are the limitations of MIM stainless steel?
Limitations include high initial tooling costs, size constraints, debinding complexity, limited material options, and potential residual porosity.
Is MIM stainless steel suitable for high-volume production?
Yes, MIM is highly cost-effective for high-volume production of stainless steel parts, making it an ideal choice for large-scale manufacturing.
Can MIM stainless steel achieve complex geometries?
Yes, MIM is well-suited for producing complex and intricate geometries that are difficult to achieve with traditional manufacturing techniques.
How does the debinding process affect MIM stainless steel parts?
The debinding process is critical and requires precise control to avoid defects, as improper debinding can lead to porosity or structural weaknesses in the final part.
Is MIM stainless steel biocompatible?
Yes, stainless steel, particularly 316L, is biocompatible and is commonly used in medical implants and surgical instruments.
Finishing Options
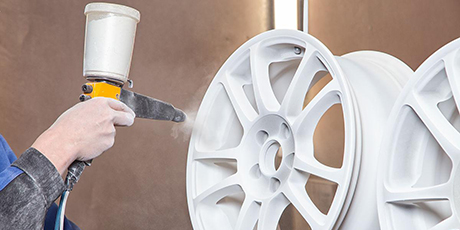
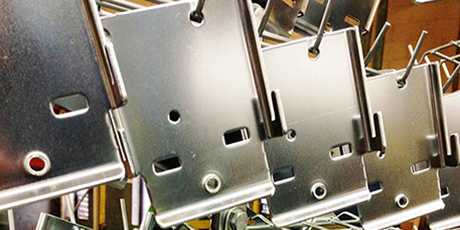
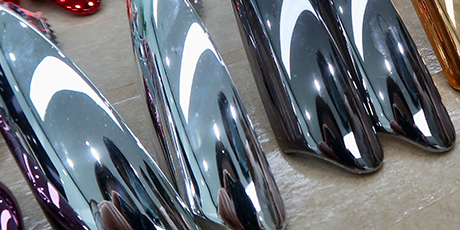
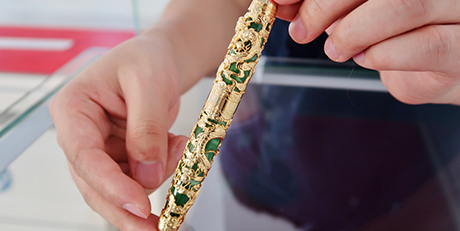
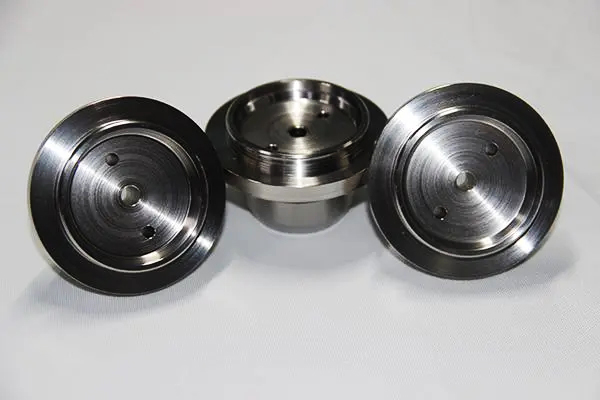
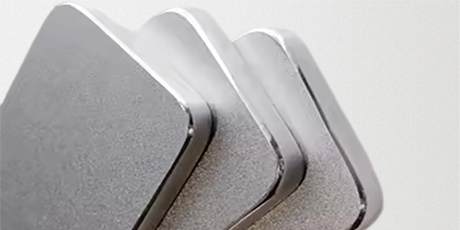
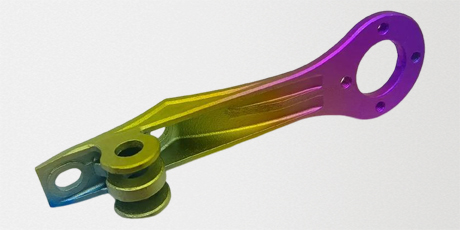
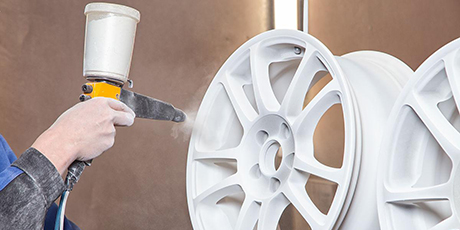
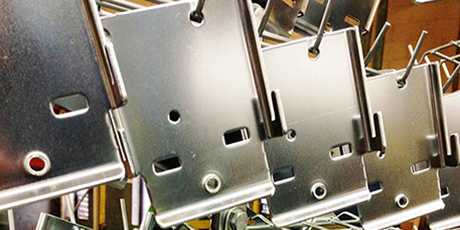
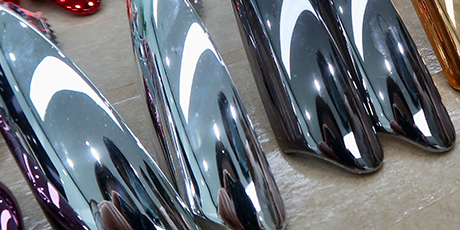
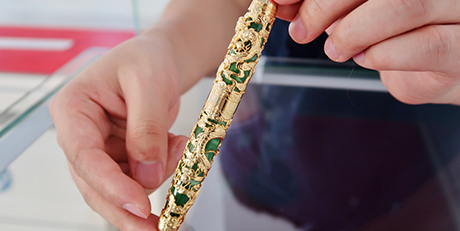
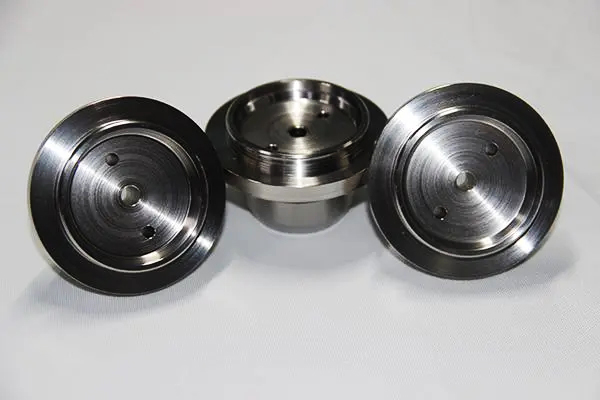
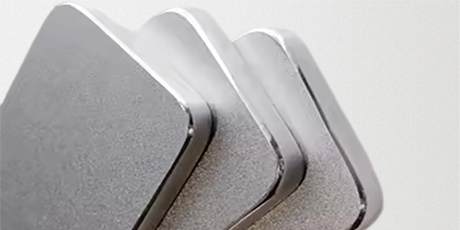
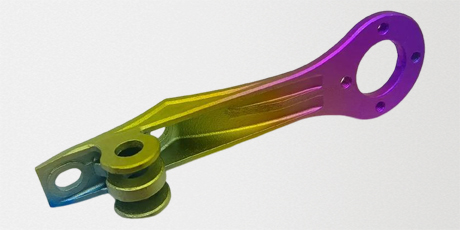
Parts Made by AutofabX
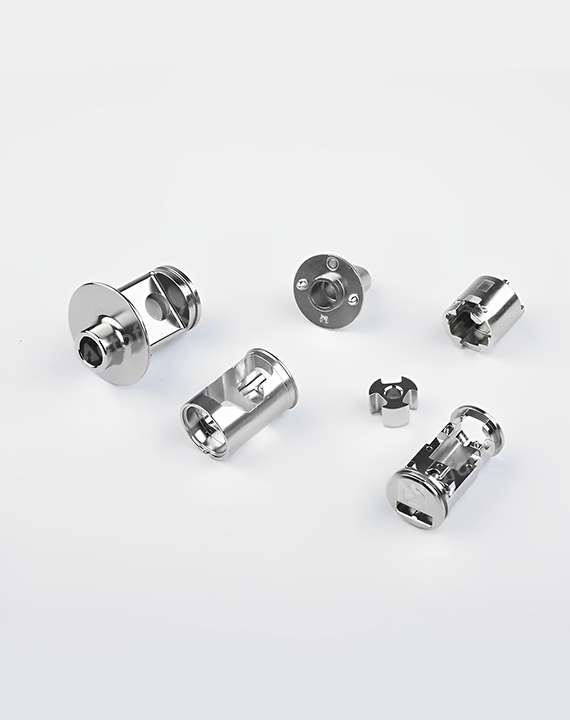
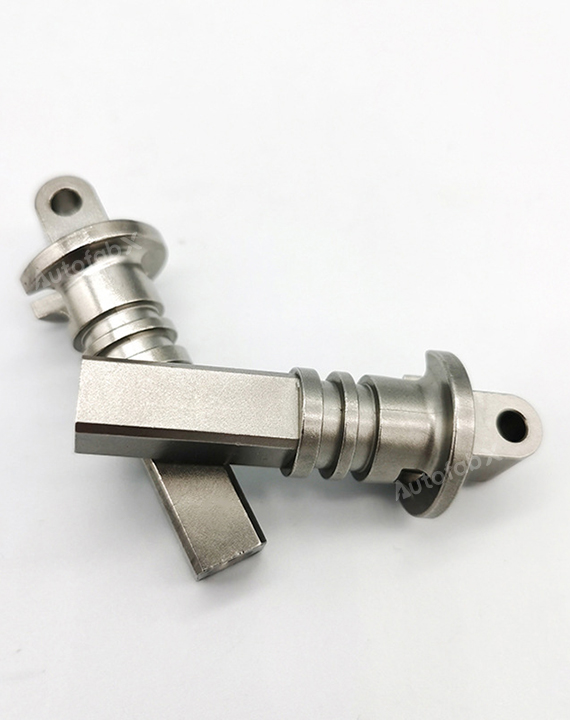
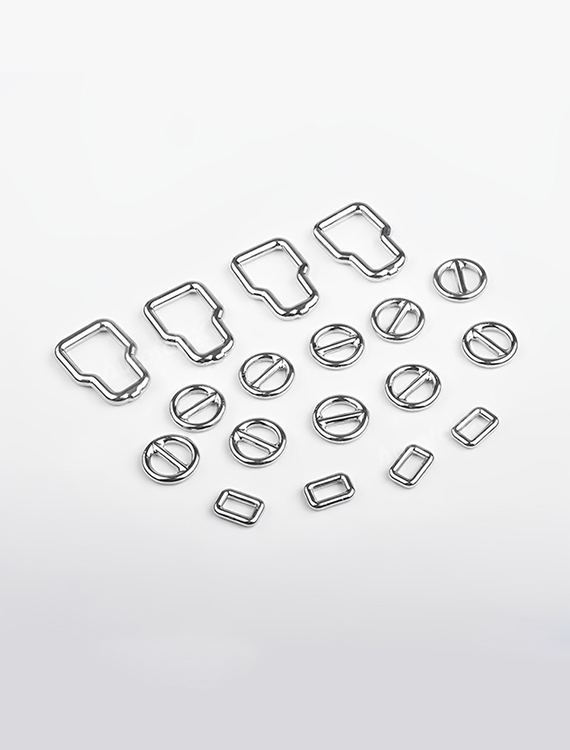