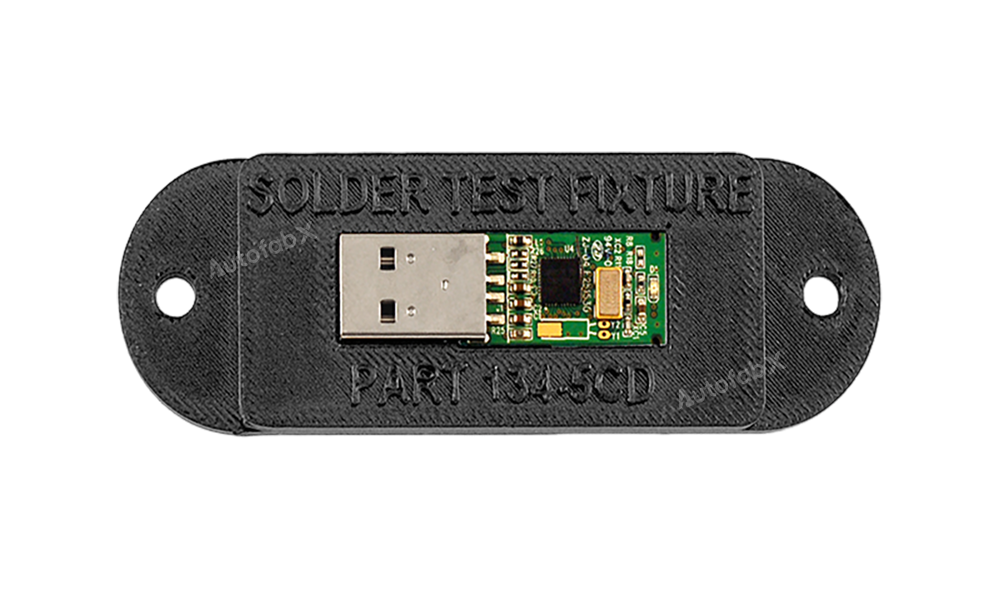
Quick Look
Density(g/cm³) | Tensile Strength | Young's Modulus | Elongation at Break | Glass Transition Temperature |
---|---|---|---|---|
1.3 | 28MPa | 47.7MPa | 8.10% | 105℃ |
About the Material
Advantages:
High Impact Strength: ABS provides good impact resistance, making it suitable for functional and load-bearing parts.
Heat Resistance: ABS can withstand moderate temperatures, making it ideal for automotive and electronic enclosures.
Post-Processing Options: ABS can be easily post-processed by sanding, painting, or acetone smoothing, allowing for a high-quality finish.
Durability: ABS is a tough material, providing good mechanical strength for a variety of applications.
Limitations:
Warping: ABS has a tendency to warp during printing, requiring a heated bed and controlled environment for successful prints.
Fumes During Printing: ABS emits fumes when heated, requiring proper ventilation during the printing process.
Lower UV Resistance: ABS is not as resistant to UV radiation, which can cause degradation when used outdoors.
Chemical Composition Table for ABS
Component | Composition |
Acrylonitrile Butadiene Styrene | 100% |
Additives (Colorants) | Varies |
Mechanical Machining Properties Table for ABS
Property | Value |
Machinability Rating | Moderate |
Cutting Speed (m/min) | 10-25 |
Tool Wear Resistance | Moderate |
Coolant Requirement | Optional |
Surface Finish Quality | High |
Design Parameters Table for FDM Printing with ABS
Maximum Bulid Size(mm) | Minimum Wall Thickness | Minimum Drill Size | Minimum Assembly Gap | Tolerance |
250*250*250,1000*610*610 | 0.6mm | 1mm | 0.2mm | ±0.3% (lower limit of ±0.1 mm) |
Industry Applications and Case Studies for FDM Printing with ABS
Automotive Industry:
Application: Production of interior components and functional prototypes.
Case Study: An automotive company used ABS to produce dashboard components, leveraging the material's heat resistance and toughness.
Consumer Electronics:
Application: Manufacturing of enclosures and housings for electronic devices.
Case Study: A consumer electronics manufacturer used ABS to create durable housings for electronic products, benefiting from its impact resistance and post-processing options.
Toys and Consumer Goods:
Application: Production of durable toys and household items.
Case Study: A toy manufacturer used ABS to create toy prototypes, taking advantage of its toughness and ability to be easily painted for a polished look.
Frequently Asked Questions (FAQs) about FDM Printing with ABS
What are the benefits of using ABS in 3D printing?
ABS offers high impact strength, heat resistance, and post-processing flexibility, making it suitable for functional parts and prototypes.
Is ABS suitable for functional parts?
Yes, ABS is ideal for functional parts that require durability, impact resistance, and moderate heat resistance.
What industries benefit from FDM printing with ABS?
Industries such as automotive, consumer electronics, and toy manufacturing benefit from the strength and versatility of ABS.
How accurate is FDM printing with ABS?
FDM printing with ABS can achieve tolerances of ±0.3 mm, which is suitable for most prototyping and functional applications.
What post-processing is required for ABS-printed parts?
Post-processing may include sanding, painting, or acetone vapor smoothing to improve the surface finish and appearance.
Can ABS be used in high-temperature environments?
ABS has a glass transition temperature of 105°C, making it suitable for moderate-temperature applications but not for high-heat environments.
How strong are ABS-printed parts?
ABS-printed parts are strong and durable, with good impact resistance, making them suitable for functional applications.
Finishing Options
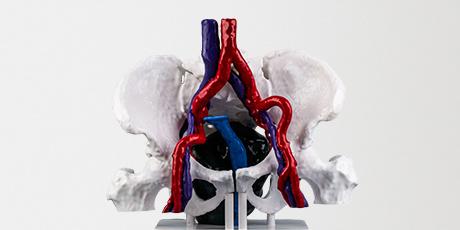
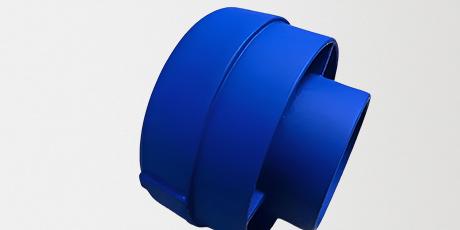
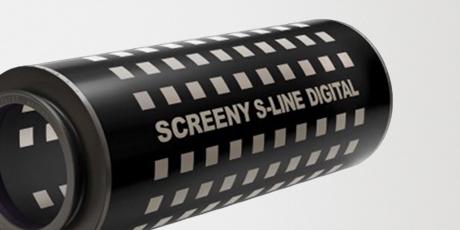
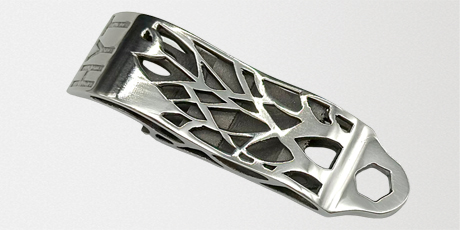
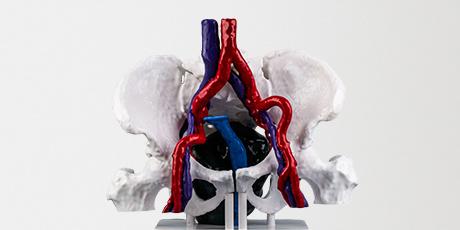
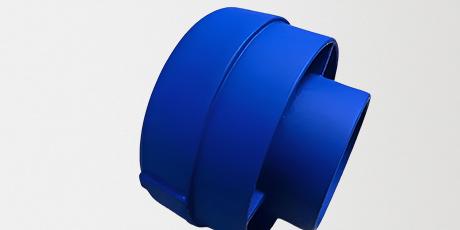
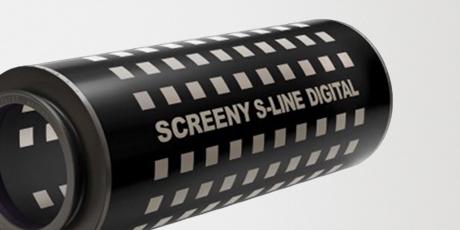
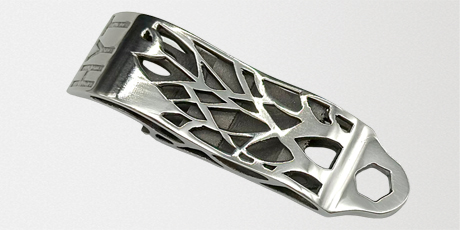
Parts Made by AutofabX
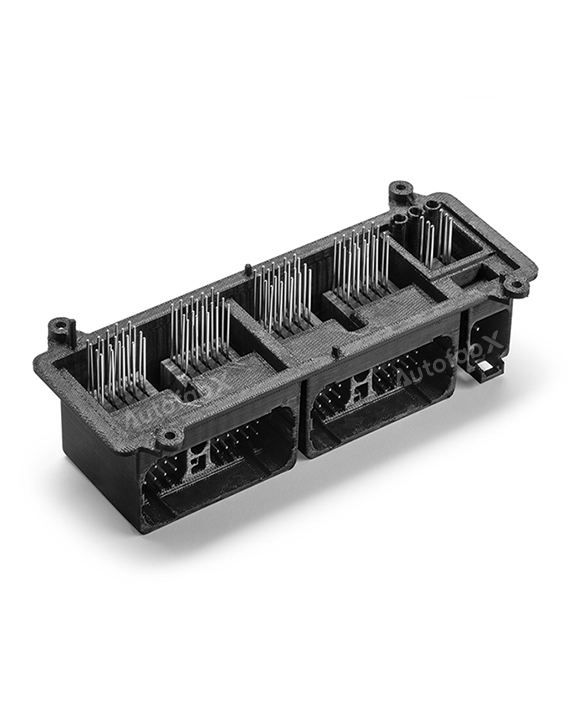
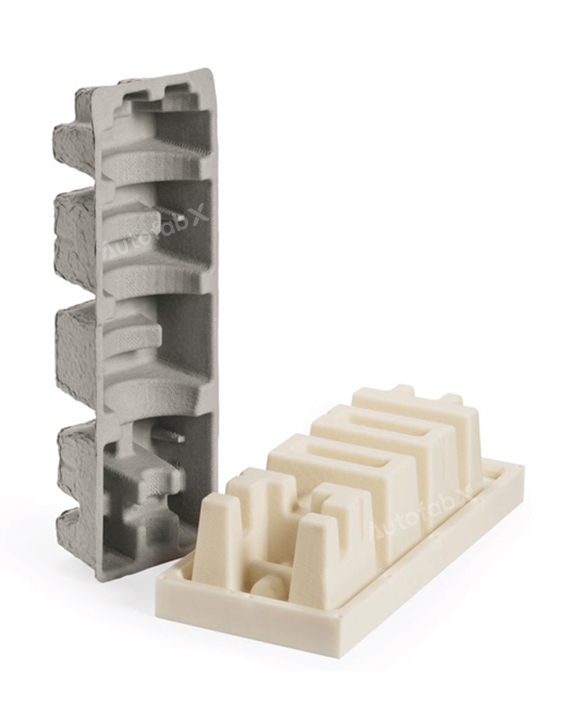
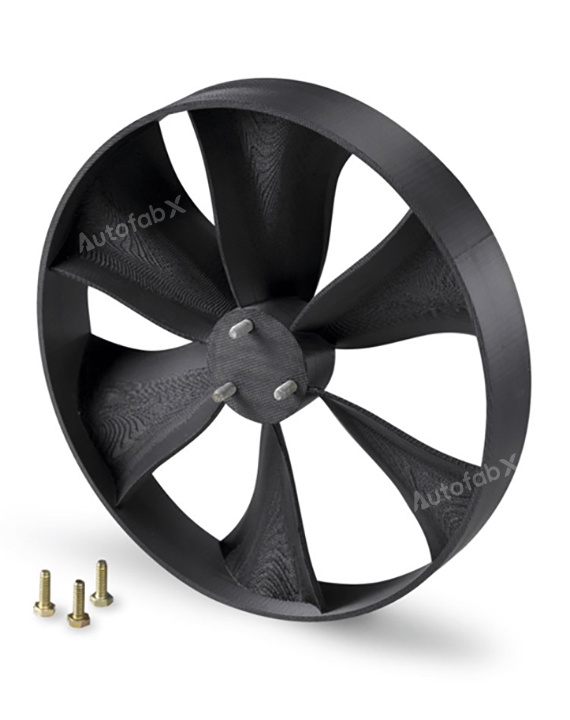