A Guide to Metal Rapid Prototyping
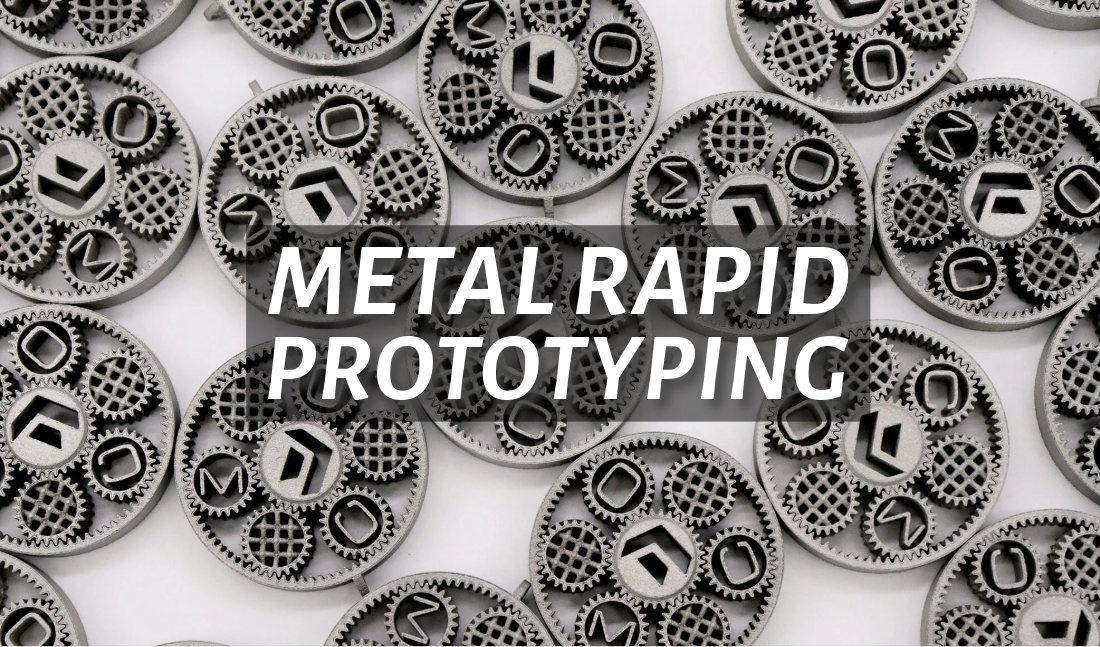
In this guide, learn how metal prototyping technologies let you bring concepts to life faster and more affordably than ever.
Introduction to Metal Prototyping
Prototyping in Manufacturing
Prototyping plays a key role in product development, allowing designers and engineers to create physical models for testing and validation.
Traditional methods can be time-consuming, especially when working with metal, but prototyping remains vital in industries that require precision and durability, such as aerospace, automotive, and medical devices.
The Rise of Metal Rapid Prototyping

“Rapid” in metal prototyping means significantly reducing the time required to create functional prototypes. This faster process is crucial for industries that need quick adjustments and faster market entry. By producing prototypes in days instead of weeks, companies can be more agile and responsive, which is essential in today’s competitive market.
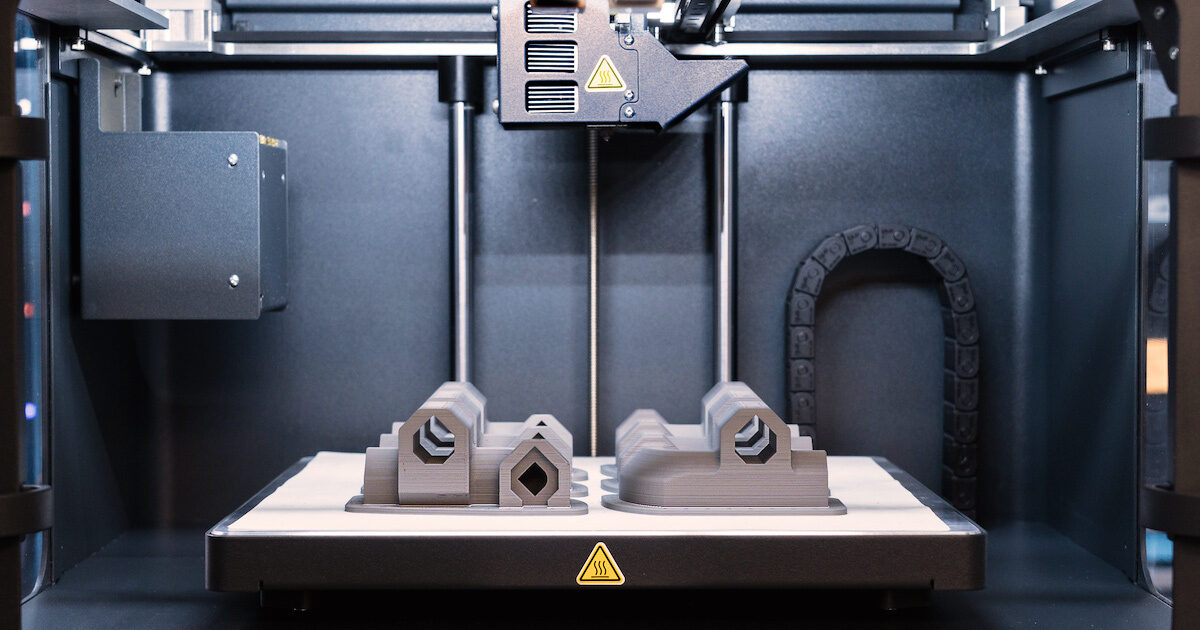
Metal rapid prototyping utilizes technologies like CNC machining, 3D printing, and casting to quickly produce metal prototypes. This approach allows engineers to focus on refining designs rather than getting bogged down in the manufacturing process, making it a game-changer in industries where performance and material strength are critical.
Types of Metal Prototyping
What is Metal Prototyping?
Metal prototyping is the process of creating early versions of a product or part using metal materials. These prototypes allow engineers and designers to test and improve their designs before full production.
Functional Prototypes
Functional prototypes are made to test how a product works under real conditions. These are built from materials similar to the final product and are used to see if the design can handle things like stress, heat, or pressure.
For example, an engine part for a car or airplane would be tested to make sure it’s strong and reliable.
Aesthetic Prototypes
Aesthetic prototypes are focused on how the product looks and feels. They may not work like the final product but are used to show the appearance, shape, and surface finish.
These prototypes are useful for design reviews or presentations to get feedback on the product’s look before moving to functional testing.
Common Materials Used in Metal Prototyping
Material | Key Features | Typical Applications |
---|---|---|
Aluminum | Lightweight, durable, corrosion-resistant, easy to machine | Aerospace, automotive, electronics |
Steel | Strong, durable, wear-resistant | Automotive, industrial equipment, heavy-duty components |
Stainless Steel | Corrosion-resistant, strong, durable | Medical devices, food processing equipment, aerospace parts |
Titanium | Lightweight, extremely strong, heat-resistant, corrosion-resistant | Aerospace, medical implants, high-performance parts |
Copper | Excellent electrical and thermal conductivity | Electronics, heat exchangers, components requiring heat dissipation |
Brass | Easy to machine, good corrosion resistance | Plumbing, electrical components, decorative products |
Magnesium | Extremely lightweight, strong, good thermal conductivity | Automotive, aerospace (for weight reduction) |
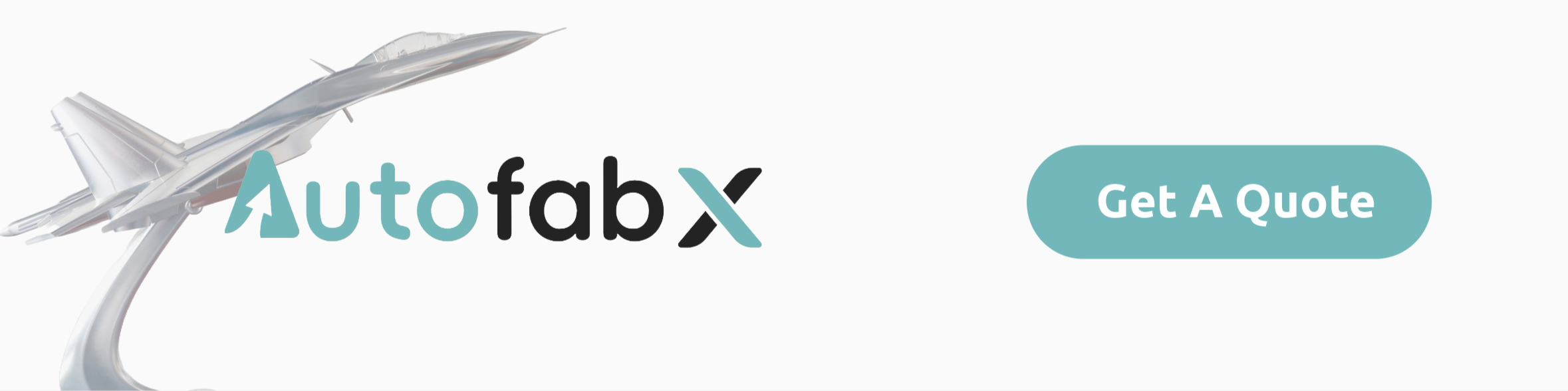
Benefits of Metal Prototyping and Metal Rapid Prototyping
Faster Product Development
Metal prototyping, especially with rapid techniques like CNC machining and 3D printing, speeds up product development. Prototypes that once took weeks to create can now be made in just days.
This helps companies test ideas faster, make improvements quickly, and get products to market sooner.
Reduced Cost and Waste
Metal rapid prototyping lowers costs in two main ways:
It avoids expensive tools and setups. Traditional methods like machining require tooling and machine setup which adds to the costs. Metal 3D printing and casting don't need these.
Less material is wasted. 3D printing technology precisely deposits only the material needed to form the prototype. This minimizes excess material compared to subtractive methods that remove unwanted material.
Customization and Flexibility
Metal prototyping provides flexibility that is valuable in certain industries. Engineers can easily customize designs and make quick changes without requiring new machinery.
This flexibility is important in industries like aerospace and medical devices, where specific designs or custom parts are often required.
Improved Functionality Testing
Metal prototypes let companies test how products will perform in real-world conditions. Companies can evaluate how their designs hold up against factors like strength, durability and temperature extremes. This helps identify any potential issues at the prototype stage, before investing in full production.
In short, metal prototyping speeds up development, lowers costs, allows for design flexibility, and improves product testing, making it a valuable tool for manufacturers.
Key Metal Prototyping Techniques
CNC Machining for Metal Prototyping

CNC (Computer Numerical Control) machining is a widely used method in metal prototyping. It shapes metal parts with precision using computer-controlled cutting tools.
This technique is ideal for creating functional prototypes that require strict specifications. It can work with various metals, including aluminum, steel, titanium, and brass, allowing for tailored prototypes.
CNC machining helps produce detailed designs quickly. It can create complex shapes and features, enhancing the functionality of the prototypes. Additionally, the fast setup and programming enable quick iterations based on testing feedback.
Advantages of CNC Machining: High precision, good surface finish, versatile with materials, and capable of complex geometries.
Disadvantages of CNC Machining: Longer setup times, material waste, and limited design options for some shapes.
Metal 3D Printing (Additive Manufacturing)
Metal 3D printing, or additive manufacturing, has transformed metal prototyping by building parts layer by layer from metal powders. Key processes include:
Direct Metal Laser Sintering (DMLS): This technique uses a laser to fuse metal powder into solid parts. It is ideal for creating intricate designs and complex internal structures, making it suitable for aerospace and medical applications.
Selective Laser Melting (SLM): Similar to DMLS, SLM fully melts the metal powder, resulting in dense and strong parts. This method is particularly effective for high-performance components that require superior mechanical properties.
Binder Jetting (BJ): This process involves depositing a binder material onto metal powder layers, which are then sintered to create solid parts. BJ is often faster and can produce larger quantities of parts, making it a cost-effective option for specific applications. Metal 3D printing offers great design flexibility, allowing for lightweight structures and complex shapes. It reduces material waste since only the needed amount of metal is used.
However, it can be more expensive, and parts might require additional finishing.
Advantages of Metal 3D Printing: Design flexibility, material efficiency, rapid prototyping, and ability to create complex internal structures.
Disadvantages of Metal 3D Printing: Higher costs, possible need for finishing, and fewer material options.
Casting for Prototyping
Casting is a key technique for producing larger and more complex metal parts. Common methods include:
Sand Casting: Uses a sand mold to shape parts, offering versatility for various designs.
Investment Casting: Involves a wax model coated with ceramic. Once the wax is removed, molten metal is poured in, allowing for precise, detailed prototypes.
Die Casting: Forces molten metal into a mold at high pressure, suitable for high-volume production of precise components.
Casting allows for intricate shapes and is cost-effective for producing multiple identical parts. However, it generally has lower precision than CNC machining or 3D printing, and mold-making can take time.
Note: 3D printing is increasingly used to create molds, which can significantly speed up the mold-making process. Additionally, 3D-printed molds can incorporate intricate features that may be difficult to achieve with traditional methods, enhancing the overall quality and functionality.
Advantages of Casting: Ability to produce complex shapes, cost-effective for large parts, and versatile with materials.
Disadvantages of Casting: Lower precision, longer lead times, and potential need for finishing.
Applications of Metal Prototyping and Rapid Prototyping
Aerospace
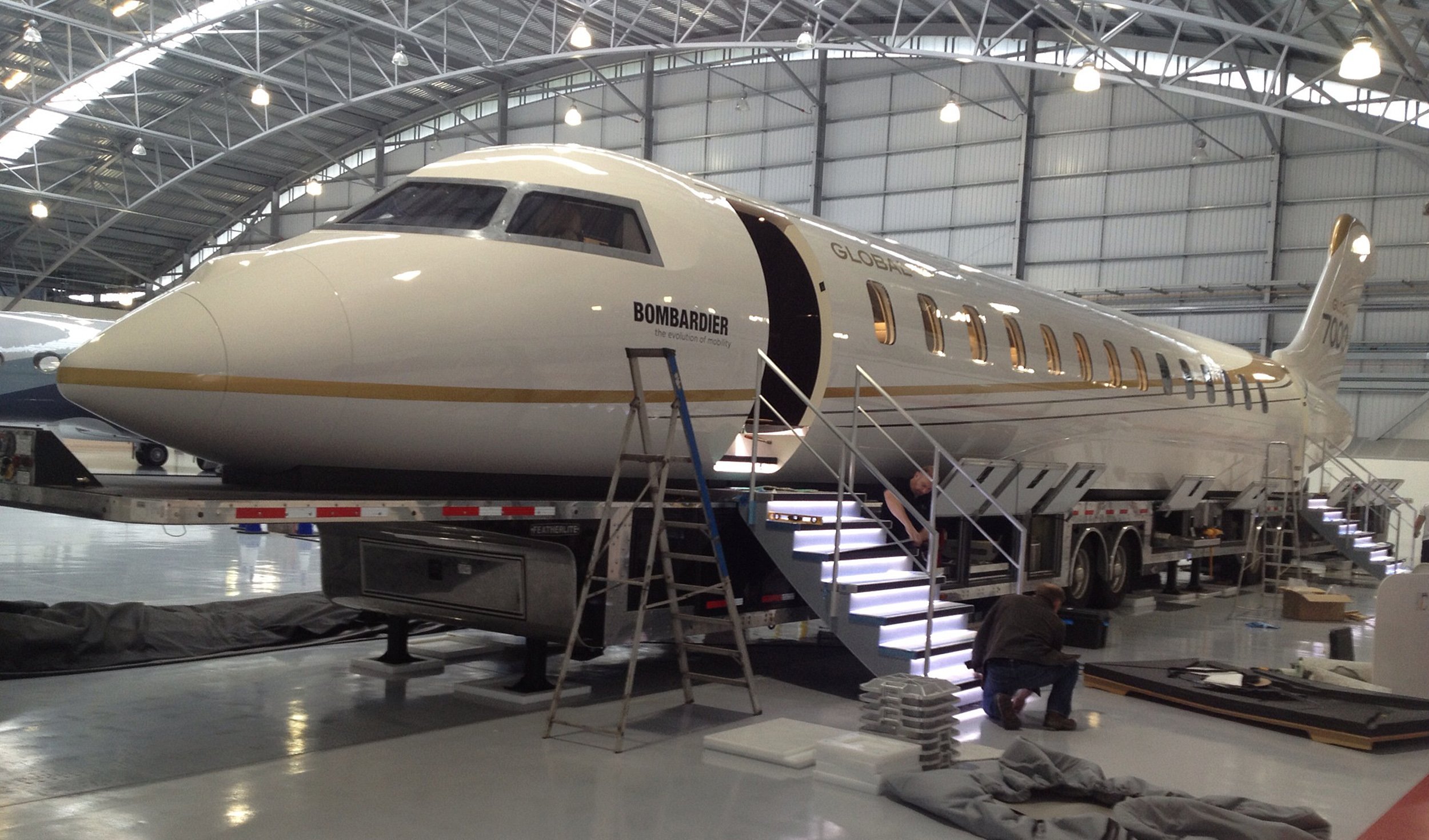

In aerospace, rapid metal prototyping enables the 3D printing of complex aircraft parts for early performance testing. This speeds up the certification process and helps identify design issues sooner.
It also allows for quick evaluation of lightweight materials such as aluminum alloys, reducing vehicle weight and improving fuel efficiency.
Automotive
Rapid prototyping helps speed up the creation of components like engine blocks and suspension parts, allowing for faster testing of new designs.
This is especially important for electric vehicles, where quick design refinement is needed to meet performance standards before mass production.
Medical Devices
In healthcare, rapid prototyping lets engineers quickly test new designs for safety and functionality. It also helps create custom solutions for individual patients, improving outcomes and advancing medical technology.
Industrial Equipment
metal rapid prototyping allows manufacturers to quickly produce and test parts for machinery and tools. It reduces downtime and helps businesses respond more quickly to market demands.
When to Use Metal Rapid Prototyping (RP)
Functional Testing, Fit, and Assembly Checks
Metal RP is highly effective when you need to test the functionality, fit, and assembly of components. It allows for the rapid creation of durable metal prototypes that mimic the final product, enabling engineers to evaluate how parts perform under real-world conditions.
Investment Casting Patterns, Molds and Cores
Metal RP can be used to create precise patterns, molds, and cores for investment casting, streamlining the casting process. 3D-printed metal patterns eliminate the need for traditional tooling, speeding up the production of molds.
Medical Devices, Aerospace & Automotive Parts
Industries such as healthcare, aerospace, and automotive benefit from metal rapid prototyping (RP) by:
Medical Devices: Quickly producing surgical tools, implants, and equipment with biocompatible materials and precise designs.
Aerospace Parts: Rapidly creating lightweight, high-strength components like engine parts and structural elements.
Automotive Components: Prototyping engine blocks, suspension parts, and other high-performance components for fit, strength, and durability testing.
Conclusion
Metal prototyping has emerged as a pivotal technology for innovation in manufacturing. Through on-demand 3D printing of functional prototypes, it has revolutionized product development workflows.
In the years ahead, it will empower greater performance, efficiencies and care across diverse applications. Metal rapid prototyping is thus well-positioned to shape the ongoing advancement of engineering and manufacturing worldwide.
AutofabX: Your Partner in Metal Rapid Prototyping
Does your project require rapid prototyping? Whether medical, automotive or aerospace, we can print prototypes that meet your strength and quality standards. Our technology lets you easily test design changes until it's perfect.
Get quotes in a minute by uploading your files, or contact us to discuss tailored solutions.
Partner with AutofabX and accelerates your product's path to market now!