CNC Precision Machining: All You Should Know
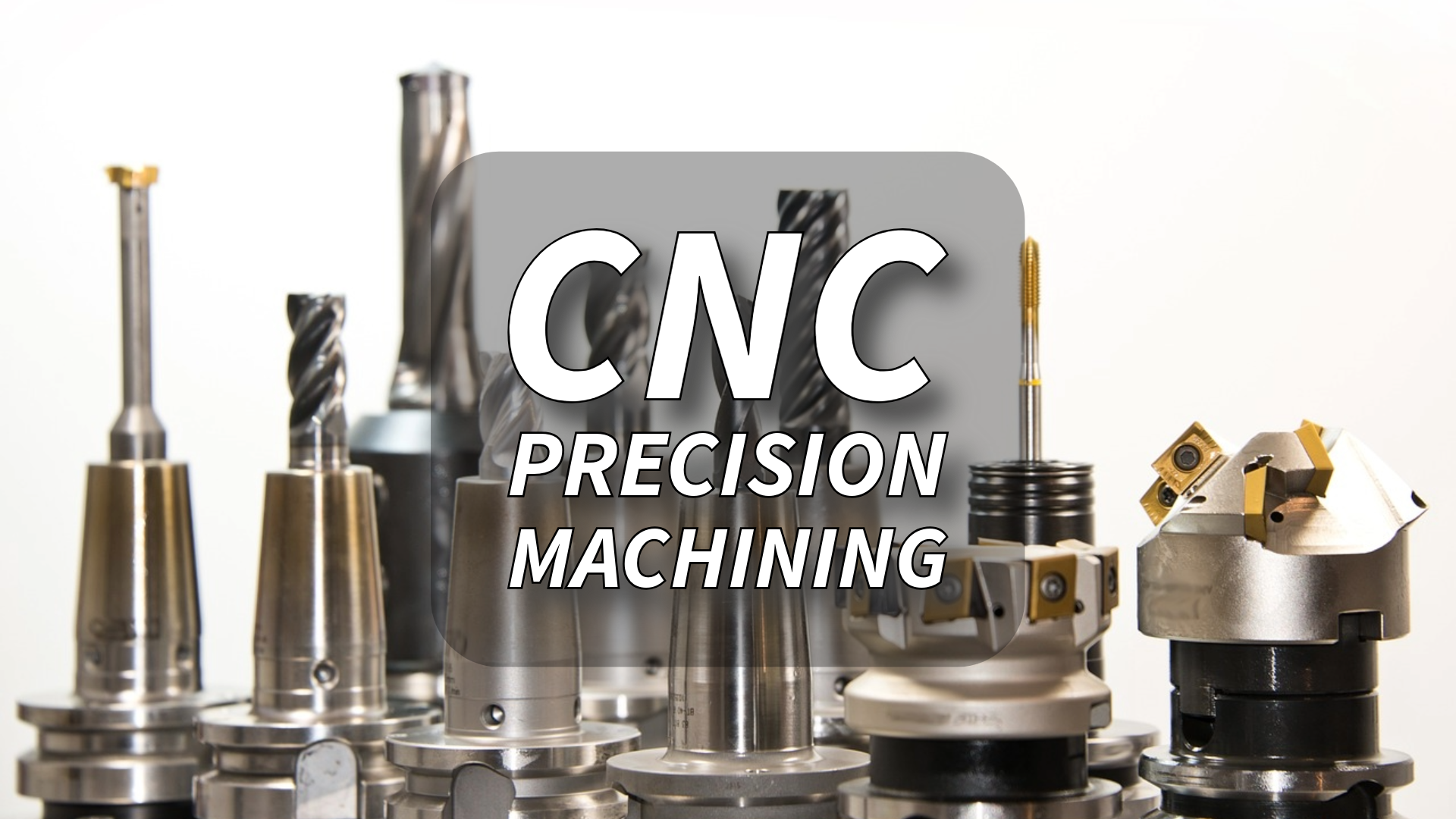
Discover the basics of CNC precision machining, including the types of machines, materials, processes, applications, and tips for achieving the best precision.
Introduction
CNC precision machining has revolutionized modern manufacturing by enabling high accuracy and consistency in creating complex parts. Through the use of computer-controlled machines, this method ensures tight tolerances and repeatable results across industries.
This article explores the fundamentals of CNC precision machining, the tools involved, materials suitable for it, and how it shapes key industries.
What Is CNC Precision Machining?
CNC precision machining uses computer-controlled machines to produce highly accurate parts by removing material from a workpiece. The process is automated through programming, ensuring precise cuts and tight tolerances.
This method is used to create parts with complex shapes and fine details, often for industries like aerospace, automotive, and medical devices, where accuracy is crucial.
Common Types and Equipment of CNC Precision Machining
CNC Process | Main Machine | Working Principle | Applicable Materials/ | Common Applications | *Cost |
---|---|---|---|---|---|
Turning | Lathe | Rotating the workpiece while the tool moves in a straight path | Cylindrical metal parts | Manufacturing shafts, pipes, and cylindrical parts | $50 - $150/h |
Milling | Milling Machine | Removing material using rotating cutting tools | Complex shapes and curved surfaces | Machining complex mechanical parts and molds | $75 - $200/h |
Drilling | Drilling Machine | Using a rotating drill bit to create holes in the workpiece | Drilling holes in plates and block materials | Drilling holes in various parts | $40 - $100/h |
Grinding | Grinding Machine | Finely grinding the workpiece surface using a grinding wheel | High-precision processing and surface finishing | Precision surface processing and mold manufacturing | $100 - $300/h |
Electrical Discharge Machining (EDM) | EDM Machine | Removing metal material through electrical discharge | Hard metals | Manufacturing molds and precision metal parts | $200 - $500/h |
Wire EDM | Wire Cut EDM Machine | Cutting metal using conductive wire and electrical discharge | Cutting complex metal parts | Cutting high-precision complex parts | $300 - $600/h |
Water Jet Cutting | Water Jet Machine | Cutting material using high-pressure water jet | Cold processing of various materials | Cutting metals, stones, and other materials | $100 - $250/h |
Plasma Cutting | Plasma Cutter | Cutting conductive metals using high-temperature plasma arc | Fast cutting of thick metal sheets | Fast cutting of thick metal plates | $50 - $150/h |
Laser Cutting | Laser Cutter | Melting or vaporizing material using a laser beam | Precise cutting of metals and non-metals | Precision manufacturing in electronics, automotive, and more | $150 - $500/h |
*NOTE: The cost ranges in the table vary based on factors like material, complexity, and setup time. Additional expenses may include tooling wear, machine maintenance, and post-processing, which can impact the overall pricing.
2-Axis vs. 3-Axis vs Multi-axis
In CNC machining, the concepts of 2-axis, 3-axis and multi-axis refer to how many directions (or axes) the machine can move in to operate the tool or workpiece, which affects the complexity of the machining process.
1. 2-Axis Machining
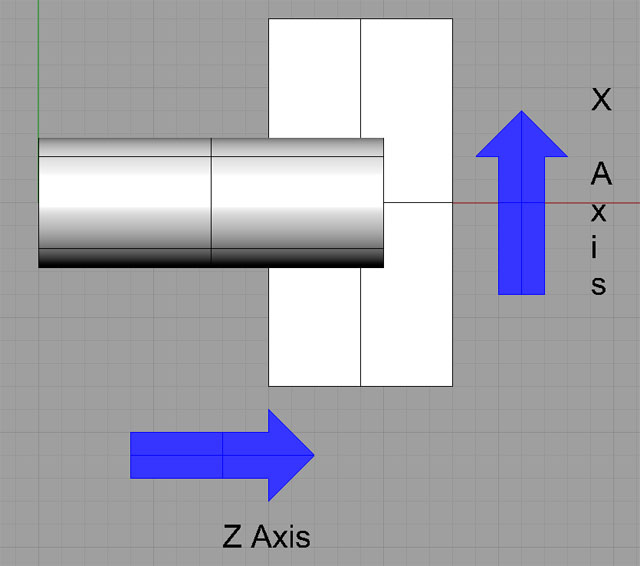
Source: cnccookbook.com
A 2-axis CNC machine can move the tool or workpiece in two directions, typically the X-axis (left and right) and Z-axis (up and down). The tool can only move along these two axes.
Application: This is used for simpler shapes, like cylindrical parts in turning operations.
Limitation: It can only perform basic cuts and is not suitable for creating complex 3D shapes.
2. 3-Axis Machining
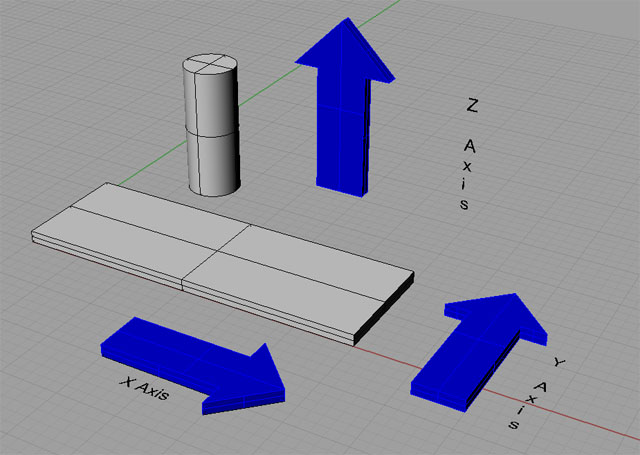
Source: cnccookbook.com
A 3-axis CNC machine can move in three directions: X-axis (left and right), Y-axis (front and back), and Z-axis (up and down). This is the most common type of CNC machining, useful for a wide range of tasks.
Application: 3-axis machines can create complex 2D shapes and some 3D shapes, such as engraving, drilling, and cutting intricate designs on flat surfaces.
Limitation: While it can handle some 3D tasks, it struggles with very complex surfaces or parts that require multi-directional machining.
3. Multi-Axis Machining
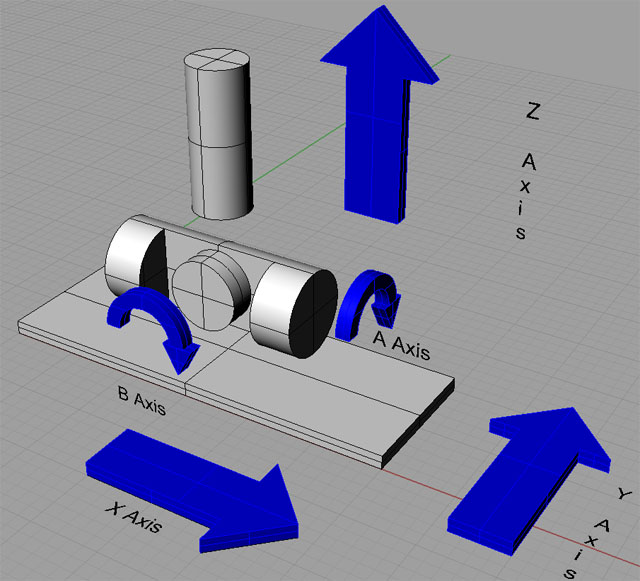
Source: cnccookbook.com
Multi-axis CNC machining refers to machines that can move in more than three directions, usually 4-axis or 5-axis. In addition to X, Y, and Z, the added axes often allow the workpiece or tool to rotate or tilt.
4-Axis: Adds an A-axis, allowing the workpiece to rotate around the X-axis, making it easier to handle curved shapes.
5-Axis: Adds both A-axis and B-axis (rotation around the Y-axis), enabling the machine to move and rotate the workpiece in multiple directions.
Application: Multi-axis machining is ideal for complex 3D parts used in industries like aerospace, automotive, and healthcare, where high precision and complex designs are required, such as turbine blades or molds.
Advantage: Multi-axis machining reduces the need to reposition the workpiece multiple times, saving time and allowing for highly detailed and accurate machining in one setup.
In summary, 2-axis and 3-axis machining are good for simpler parts, while multi-axis machining is necessary for more complex shapes and high-precision work.
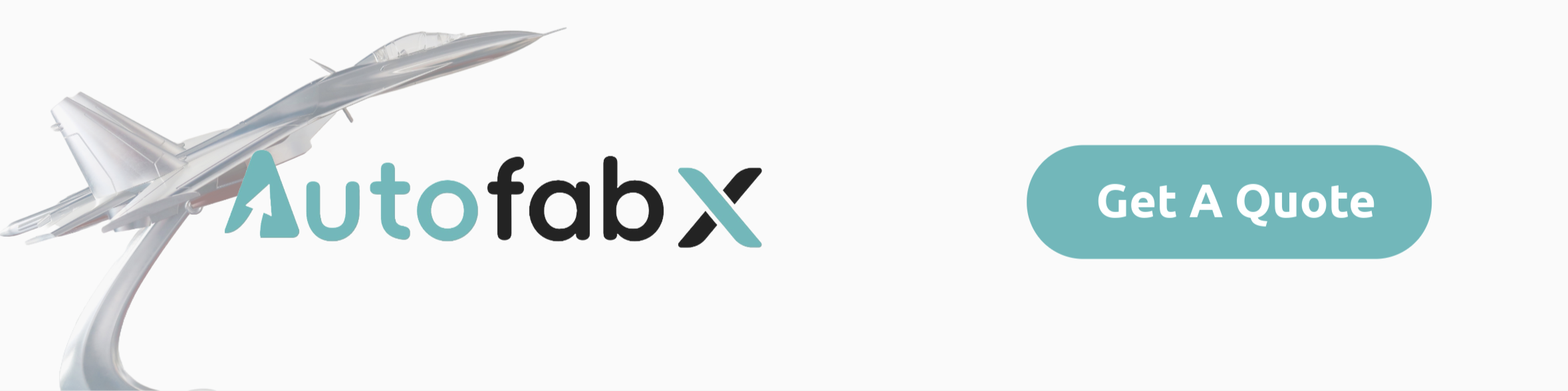
Common Materials Suitable for CNC Precision Machining
Metals
In metal CNC machining, the metals’ properties can affect both the efficiency of the process and the final product’s quality. Different metals have unique machining needs; for example, harder metals require the use of carbide or diamond-coated tools, along with a good cooling system to handle heat.
The followings are the common metals used for CNC precision machining. And you can visit the CNC Machining page to check all available materials provided by AutofabX.
Aluminum
Steel
Stainless Steel
Titanium
Copper
Brass C360 C260
Bronze C932 and C954
Inconel 718
Monel 400
Plastics
When CNC machining plastics, it's important to manage heat to prevent material deformation. Choosing the right cutting tools, controlling machining speed, and using coolant helps maintain precision and surface quality.
Here we have listed the commonly-used plastics in CNC machining.
Nylon 6
Nylon 6/6
ABS (Acrylonitrile Butadiene Styrene)
HDPE
PC (Polycarbonate)
PE (Polyethylene)
POM (Polyoxymethylene)
PMMA (Polymethyl Methacrylate)
PP (Polypropylene)
PU (Polyurethane)
PVC (Polyvinyl Chloride)
PA6/PA66 (Polyamide 6/ Polyamide 66)
PTFE (Polytetrafluoroethylene)
PEEK (Polyetheretherketone)
Composites
Except for metals and plastics, composites, combining two or more constituents, are increasingly popular in CNC machining for their balance of strength, weight, and durability and often outperform metals in applications where lightweight yet strong parts are needed.
Here we have named the common composites used in cnc machining.
Synthetic stone (CDM) Bakelite PF FR4 Epoxy Fiberglass ZrO2 Ceramic
Step-by-Step Guide to the CNC Precision Machining Process
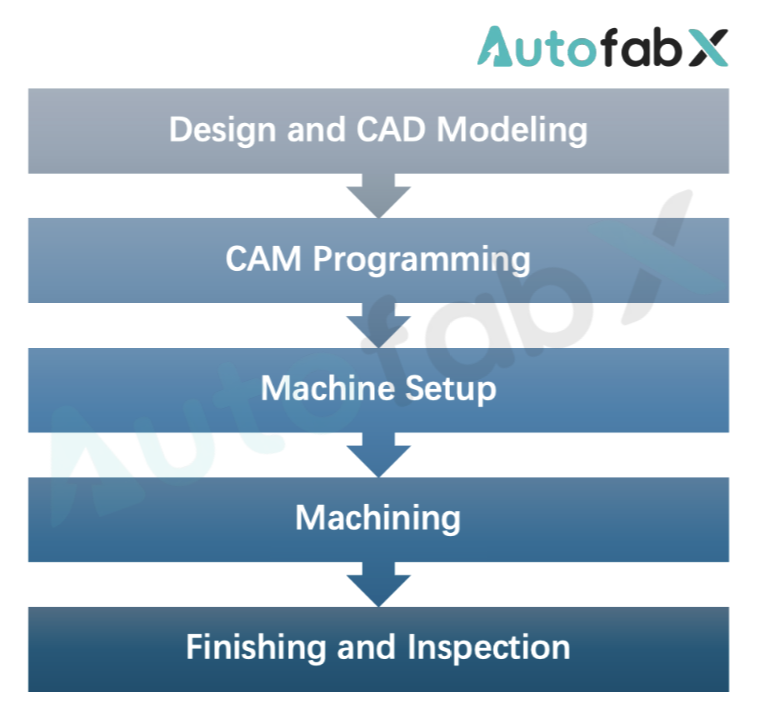
Design and CAD Modeling The first step involves creating a 3D CAD model, detailing the dimensions, geometry, and specifications of the part to be machined. This model serves as the blueprint for the entire process.
CAM Programming The CAD model is imported into CAM software, where tool paths are generated. These instructions (in G-code or M-code) tell the machine how to move, cut, and shape the material.
G-code (Geometric Code): This is the programming language that controls the movement of the CNC machine. G-code commands tell the machine how to move, including positioning (X, Y, Z axes), feed rate, and toolpath. For example: G00: Rapid positioning G01: Linear feed motion
M-code (Miscellaneous Code): M-code controls auxiliary functions like starting or stopping the spindle, coolant, and tool changes. For example: M03: Start the spindle M05: Stop the spindle M08: Coolant on To learn more about G & M code, you can read this article: G & M Codes: The Secret Language of CNC Machines
Machine Setup The CNC machine is configured with the right tools for the job. This includes selecting appropriate cutting tools, mounting the workpiece securely on the machine bed or fixture, and adjusting parameters such as speed and feed rates.
Machining The CNC machine follows the programmed instructions to remove material from the workpiece. This can include operations like milling, turning, drilling, or grinding, depending on the complexity of the part. The machine’s movements are precise, ensuring the part’s exact dimensions.
Finishing and Inspection After machining, the part may undergo additional finishing processes like deburring, polishing, or surface treatment. Finally, it is inspected to ensure all tolerances, dimensions, and surface qualities meet the specified requirements, often using tools like calipers or coordinate measuring machines (CMM).
CNC Machining Tolerance Considerations
In CNC precision machining, achieving tight tolerances is critical, especially in industries like aerospace and medical devices where accuracy is essential. To ensure precision, factors like material properties, part complexity, tool wear and stability and thermal expansion must be carefully managed. Here we have compared the standard tolerance considerations and the advanced options that AutofabX can offer with sophisticated CNC machines and proper quality control .
Feature | Standard | Advanced Option |
---|---|---|
Tolerance | ±0.005 inch (±0.127mm) | ±0.0005 inch (±0.0127mm) |
Surface Roughness (Ra) | 125uin (3.2μm) | Up to 16uin (0.4μm) |
Lead Time | 7-12 days | ==Contact us== for details. |
Machining Techniques | Milling, Turning, Routing, Drilling, Grinding, EDM, Wire EDM | 3 aixs, 4 axis, 5 axis machining |
Inspection | Standard Report (Free) | CMM Inspection or Third Party Inspection (Fee Required) |
Tips for CNC Precision Machining
When performing precision machining, considering certain details can significantly enhance the accuracy of the final product. Here are some tips to help you achieve better results.
Feature | Recommendation | Reason |
---|---|---|
Tolerances | Use tight tolerances only when necessary | Tighter tolerances increase machining time and costs. |
Text | Avoid small or raised text | Adding text increases costs, especially if it's small. |
Walls | Avoid tall and thin walls (usually 0.5-1 mm minimum wall thickness for metals) | Thin walls are prone to warping and breaking during machining. |
Internal Corners | Minimize sharp corners, use larger radii | CNC tools are cylindrical, so larger radii ensure smoother cuts and reduce tool wear. |
Tool Sizes | Design using standard tool sizes | Custom tools are expensive and increase lead times. |
Feature Alignment | Maximize alignment with machine axes | Aligning features reduces tool changes and setup times, lowering costs and preventing fitting issues in assemblies. |
Key Applications and Industries of CNC Precision Parts
CNC precision parts are essential across various industries that demand high accuracy and consistency. Sectors like aerospace, automotive, medical devices, and electronics rely on CNC machining for creating precise, complex components. Here let’s explore the key industries and applications.
Aerospace: Used for manufacturing engine components, turbine blades, and structural parts.
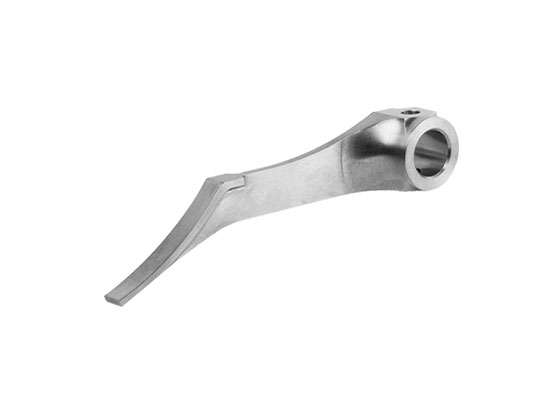
Source: tmetalparts.com
Automotive: CNC machining produces engine blocks, transmission parts, and custom car components.
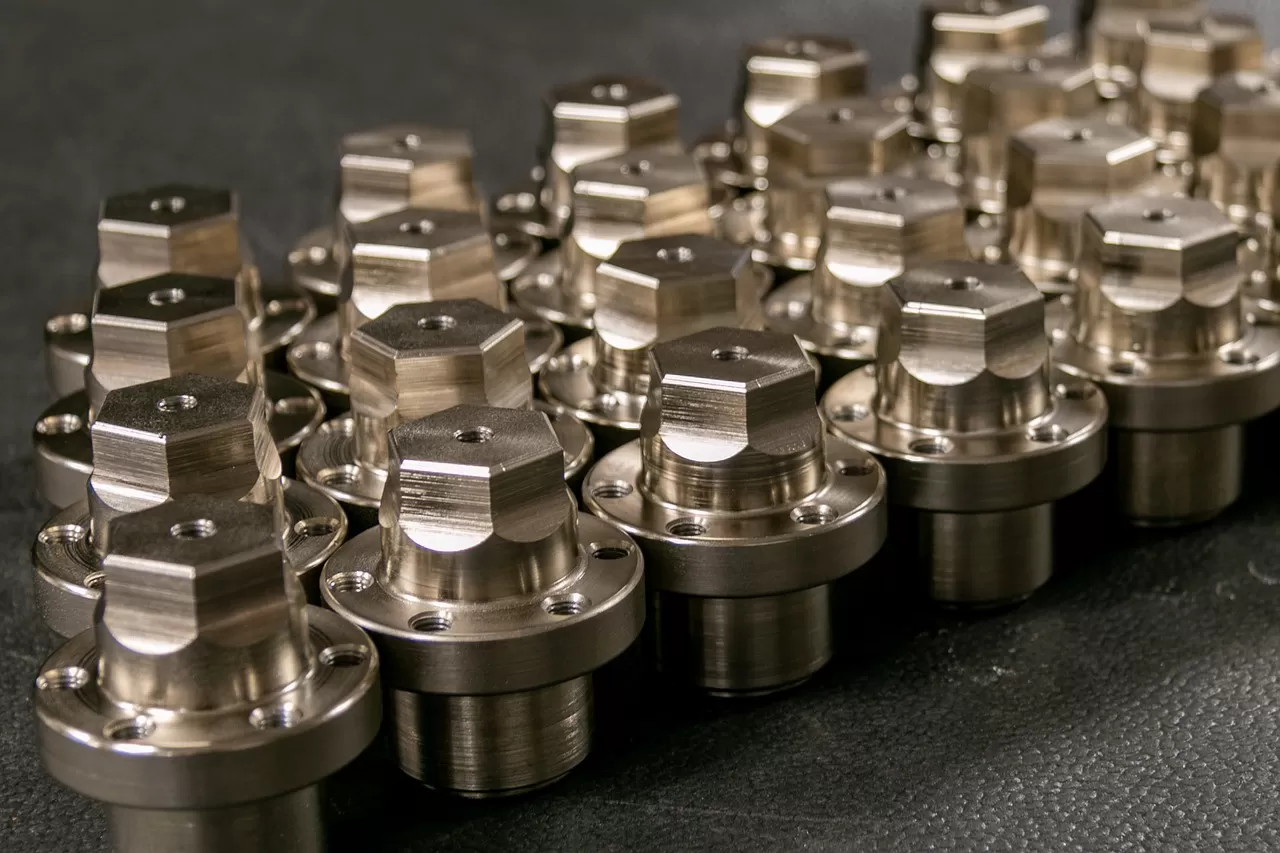
Source: sacher-cnc.com
Medical Devices: Precision parts for surgical instruments, implants, and diagnostic devices.
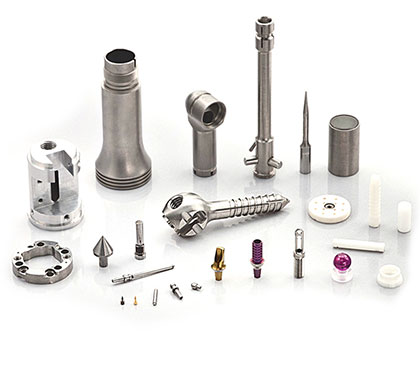
Source: dajinprecision.com
Electronics: CNC is used for creating precise enclosures, connectors, and internal parts.
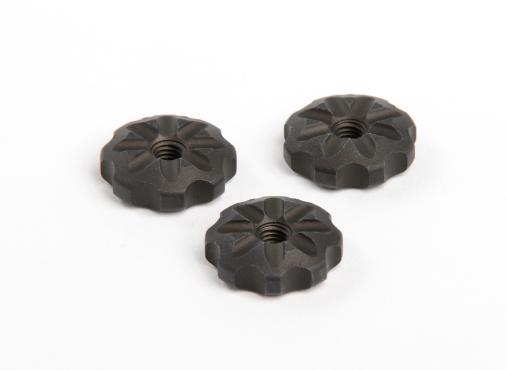
Source: dajinprecision.com
Defense and Military: For specialized equipment and high-performance components.
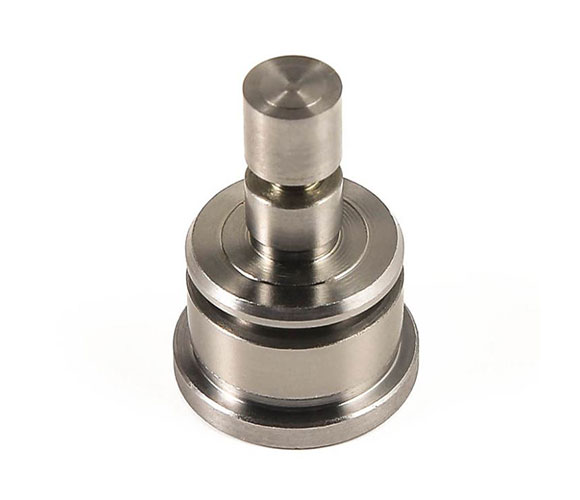
Source: panekprecision.com
FAQs
How precise can CNC machines be?
Tolerance: CNC machines can achieve tolerances as small as ±0.0002 in (±0.00508 mm). The standard tolerance limit is about ±0.005 in (0.127 mm).
What are the CNC machine file formats?
The file formats can be divided into 2D and 3D categories: 2D: G-code, DWG, DXF, PDF 3D: STEP, STP, IGS
What is the difference between accuracy and precision in machining?
Accuracy refers to how close a measurement is to the true value, while precision indicates how consistently a machine can produce the same measurement repeatedly. Here's an analogy:
Accuracy: Imagine you're aiming for a bullseye on a dartboard. If your darts land close to the bullseye but in different spots, you are accurate but not precise.
Precision: If all your darts land in the same spot, but far from the bullseye, you are precise but not accurate. In machining, accuracy ensures the part dimensions are close to the desired size, while precision ensures the machine can produce consistent results across multiple parts.
Achieve Precision with CNC Machining at AutofabX
When precision is paramount, trust AutofabX's CNC machining expertise. We have the lathes, mills and multi-axis machines to manufacture to tight tolerances and smooth finishes.
As a full-service provider, we support the complete project lifecycle within our ISO-certified facility. We can produce parts from prototypes to mass quantities.
Get an instant quote or contact us to discuss your project's requirements!